

The thermal cycle and organized deformation associated with the forging process result in grain refinement and controlled metallurgical recrystallization. Advantages to forgings include retention of uniformity of composition and crystalline structure within the material. The Better Optionįorging involves the application of thermal and mechanical energy to steel billets causing the material to change shape while remaining in the solid state. However, forgings will have more potential strength. So long as care is exercised, cast parts can be produced in quantity and require minimal surface finishing. Filling the mold with molten steel vaporizes and displaces the filler. Investment casting dates back at least 5,000 years and involves using some type of solid 3-D pattern made from something like wax within a ceramic mold. This technique can minimize finish machining requirements but results in a part that might not be as durable as a comparable forged component. Steel casting involves pouring molten steel into a mold. Castings can also include microscopic porosities from little gas bubbles or other impurities retained within the metallic structure that can cause potential weak spots. However, cast parts end up with a random crystalline microstructure that makes them potentially weaker than forgings. Casting is amenable to the manufacture of complex shapes and particularly large parts. Steel casting involves pouring molten steel into a mold and allowing it to harden as it cools. This hematite mined in Brazil is a typical example.
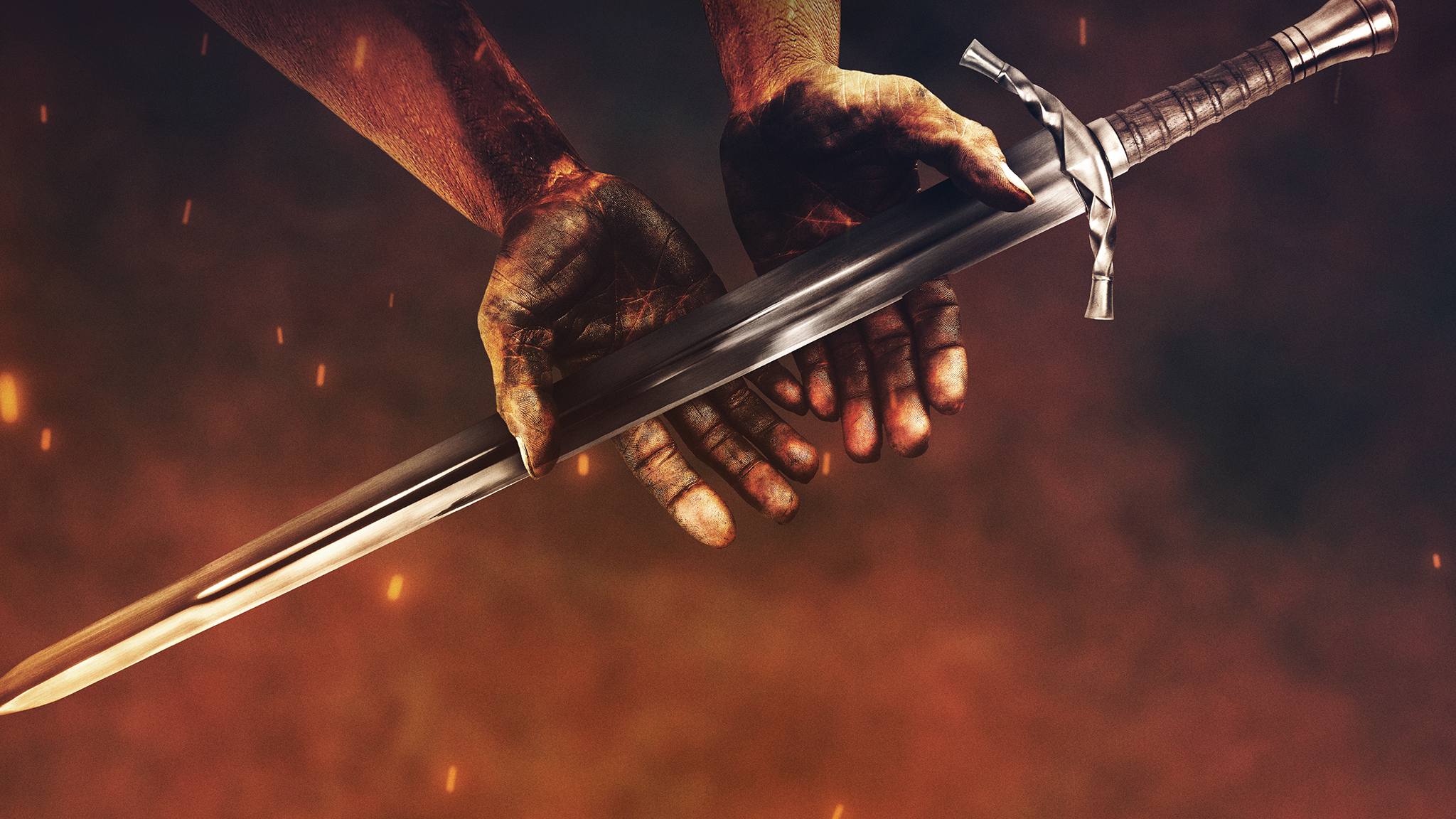
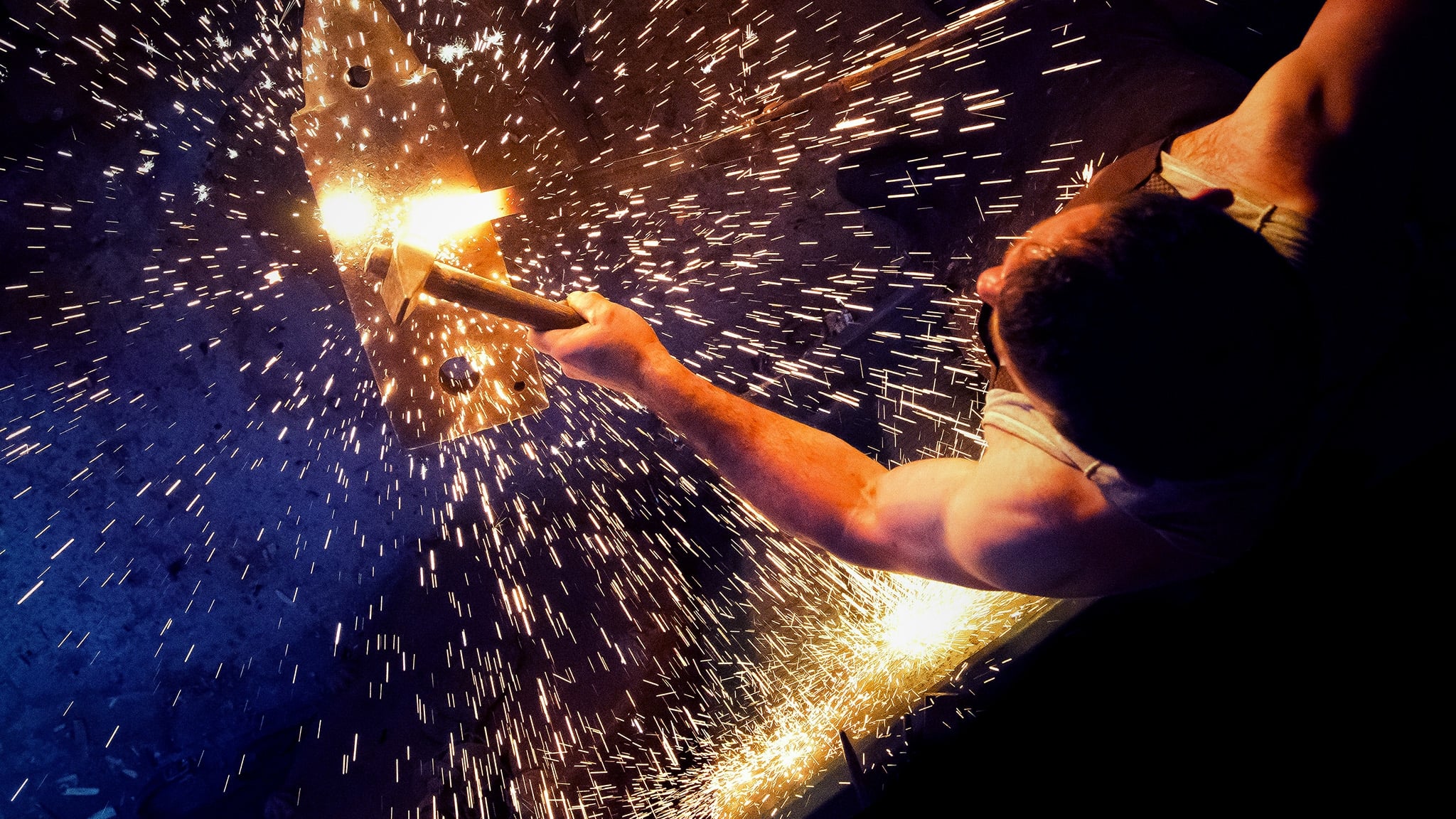
Iron in the form of various ores is one of the most common elements in the earth’s crust. Frequently, manufacturing processes come down to balancing function and durability against cost. Optimizing these properties is critical to producing quality gun parts that will last. This microstructure determines such characteristics as strength, ductility and wear resistance. Steel actually has a complicated internal microcrystalline structure that has been exhaustively studied. Steel is not the amorphous homogenous stuff it appears to be on the outside. You may have heard of cast versus forged steel, but wondered what the difference was. Not least among them is making gun parts. That stuff can be used to do some of the most wonderful things. However, mix that iron with a little special sauce like carbon, chromium, nickel and the like, and you get various steels. In its elemental state, iron reacts quickly with oxygen and water to form oxides in the form of rust. It melts at 2,800° F and boils at 5,182° F. With an atomic number of 26 and an atomic weight of 55.845, iron is extraordinarily versatile stuff. When it comes to strength in a steel part, it’s hard to top forging like the drop hammer forging process shown here. So, let’s dive into this subject here and see if we can make some sense of it all. The quality of the materials and construction of your firearm is of the utmost importance. Ever wondered what it means when you read about gun parts being “cast” or “forged”? Metal is metal, so it shouldn’t matter, right? Wrong.
